Example: if you use 1 “dia”. End milling cutter. 100 “WOC, WOC = 10% of cutting diameter.
Using the above chart, the chip thickness factor = 1.7.
If the thickness of a chip. What is needed is the feeding speed. 0085 “(. It should be programmed on the machine tool.
Or the adjusted per tooth (AFPT)= ideal chip thickness x slice dilution factor (from the chart).
Spiral interpolation large diameter hole manufacturing
When the spiral interpolation method is used, the production of large diameter hole can be quickly and easily. This technique is similar to the movement of threads in all three axes (X, Y, and Z). Unlike thread milling, it is introduced without any kind of starting hole.
The tool simply locates in the inner diameter of the hole, and from there it begins its spiral by reaching down to the final depth to achieve complete removal of the material. This kind of smooth operation avoids the high – horsepower consumption characteristic of large diameter hole. The quick and simple process provides an additional advantage that allows many different hole sizes to be generated with the same diameter tool. The hole size changes are in programming.
Safety measures for metal cutting and grinding
Modern metal cutting techniques may use very high operating parameters (speed, feed, cutting depth, etc.). This creates the possibility of flight chips and debris, and can cause tools to break down for a variety of reasons. Therefore, any metal cutting operation should be performed in a completely closed (shielded) environment to prevent damage from flying objects. After purchase, DPA does not bear any loss, damage or expense of any use or disposal of our products.
Grinding produces harmful dust. To avoid adverse health effects, use appropriate ventilation and reading material safety data sheets first.
Biaxial power scraping guide
Scrape off any obvious scar, milling, turning, grinding, etc., caused by the Angle of 45 °. Use long trips and short hard blades.
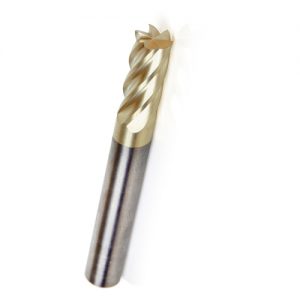